Why Refinery Digital Transformation Is Too Important to Delay
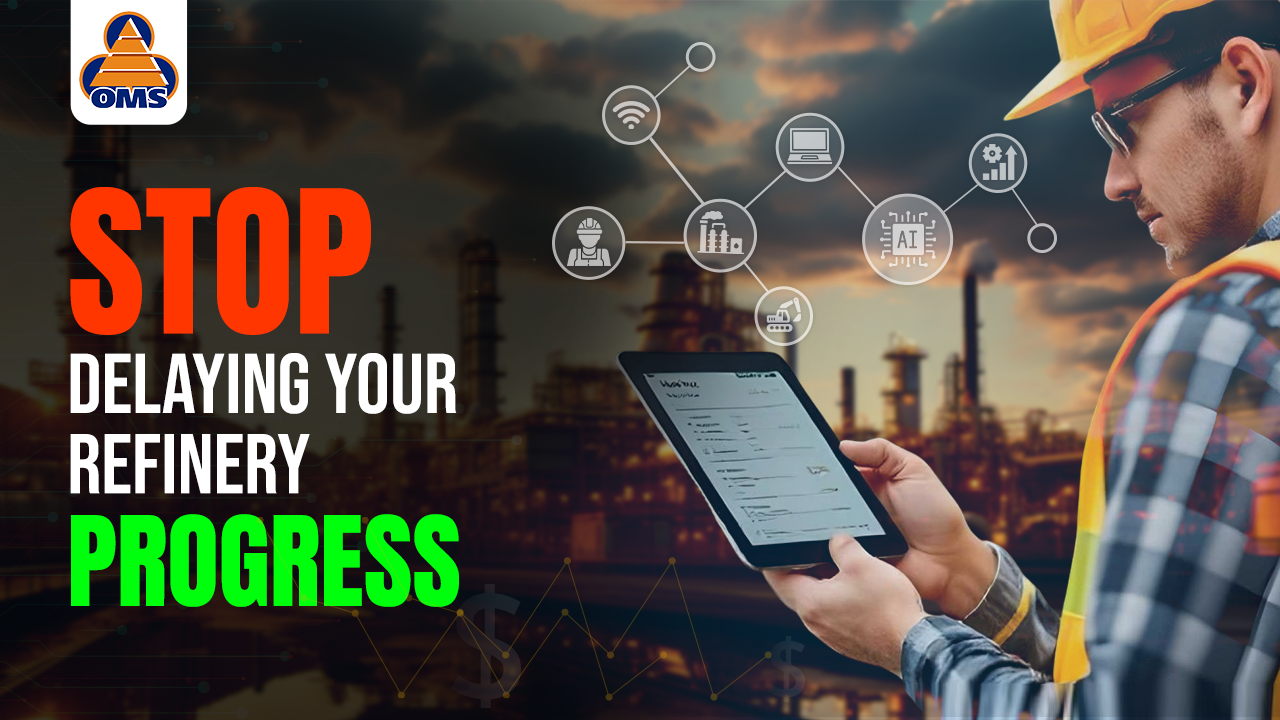
Refinery Digital transformation is now a necessity, not a future goal. In today’s fast-moving energy landscape, standing still means falling behind. Outdated technology increases risk, drains revenue, and invites regulatory trouble. The hidden cost of “doing nothing” keeps growing. This blog explores how digital delays hurt performance—and how OMS helps turn those risks into smart, value-driven upgrades.
Delaying Action? The Real Cost Behind Refinery Digital Transformation Inertia
Digital transformation is no longer a futuristic ambition but a present-day necessity in the refining sector. According to Bain & Company’s detailed analysis on Energy Transition and Digitalization, refineries that delay modernization risk falling into what the report calls the “digital laggards’ trap”—a cycle where outdated systems not only limit operational efficiency but also block access to decarbonization initiatives, advanced trading models, and low-carbon innovation.
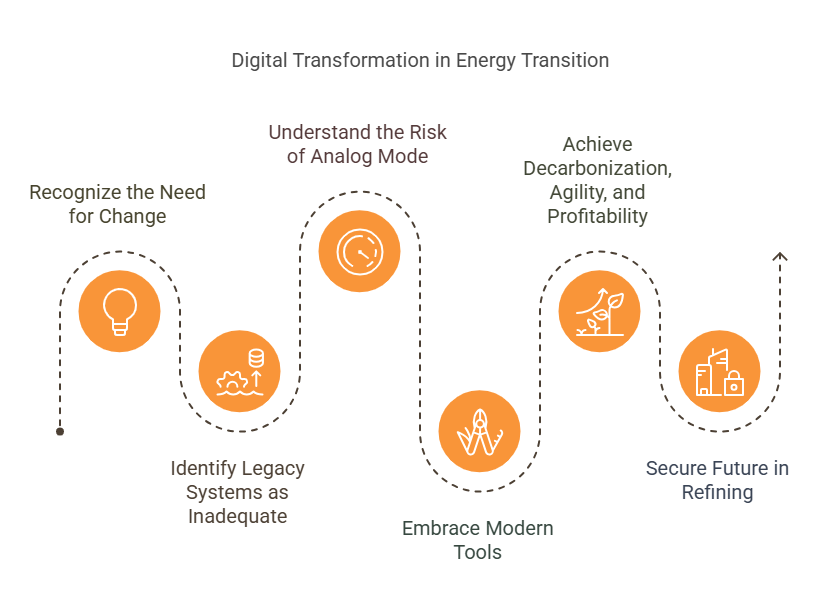
As the industry shifts toward cleaner fuels, circular operations, and stricter emissions rules, digital tools are becoming essential for staying compliant and competitive. But many refineries still rely on legacy systems designed for a more linear, analog world. These outdated setups can’t keep up with the fast-moving demands of today’s energy transition. Without core technologies like advanced process controls, real-time analytics, and integrated digital platforms, these facilities risk being left behind in the push toward a low-carbon future.
“Digital laggards will struggle to survive as energy transition and data-driven decision-making reshape the refinery business model.”
— Bain & Company, Refining in Transition
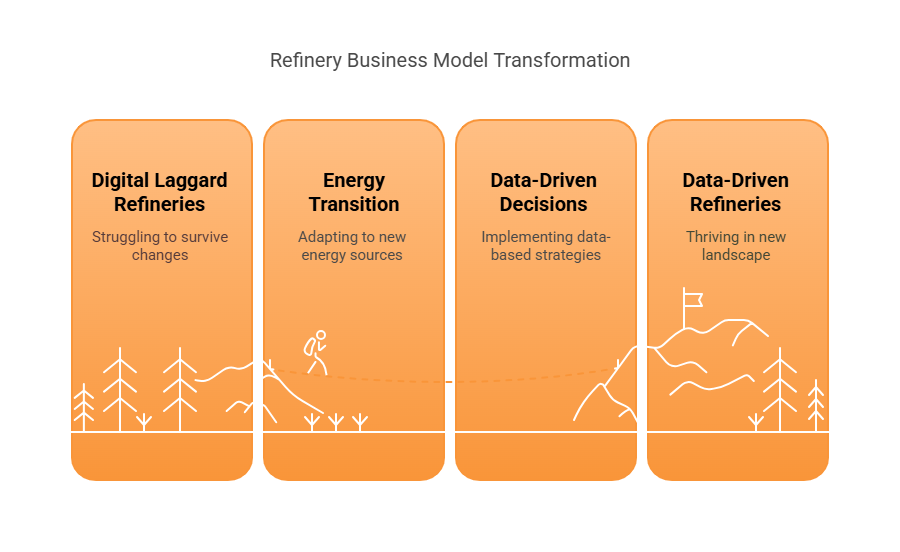
The impact of falling behind goes far beyond just missing environmental goals. Refineries stuck with outdated systems also lose their edge in the market. They struggle to adapt quickly, miss out on optimizing throughput, and often can’t tap into high-margin trading opportunities. This makes them less appealing to investors and partners who care about ESG performance.
That’s where OMS comes in.
- Its Digital Maturity and Performance Gap Assessment is explicitly designed for refineries.
- It examines your current technology setup and compares it to industry standards and decarbonization goals. Instead of pushing expensive, large-scale changes, OMS focuses on smart, low-risk upgrades—like improving blend logic or adding analytics tools—that make a difference.
The result? A custom roadmap that helps you modernize safely, strategically, and without disrupting operations.
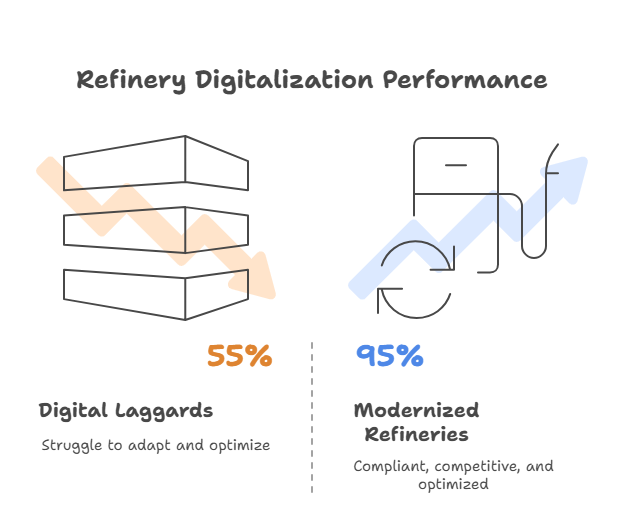
Hidden Losses That Add Up: Why Postponing Refinery Digital Transformation Is Expensive
Beyond visible inefficiencies lies a massive layer of hidden costs, often overlooked until they reach crisis levels.
According to a study by Emerson, facilities processing 250,000 barrels per day lose an average of $12.3 million per year due to outdated technology and a lack of Industrial Internet of Things (IIoT) integration. These losses manifest in wasted energy, high maintenance costs, delayed blending, and poor scheduling decisions.
- OMS helps close that gap with its ROI modeling services, which closely examine off-site systems, blending setups, and utility use.
- By working with the data you already have and running digital retrofit simulations, OMS often finds hidden savings of $0.20 to $0.40 per barrel just by upgrading software and logic layers—no new hardware is needed.
- It’s a smart, cost-effective way to boost performance where it counts.
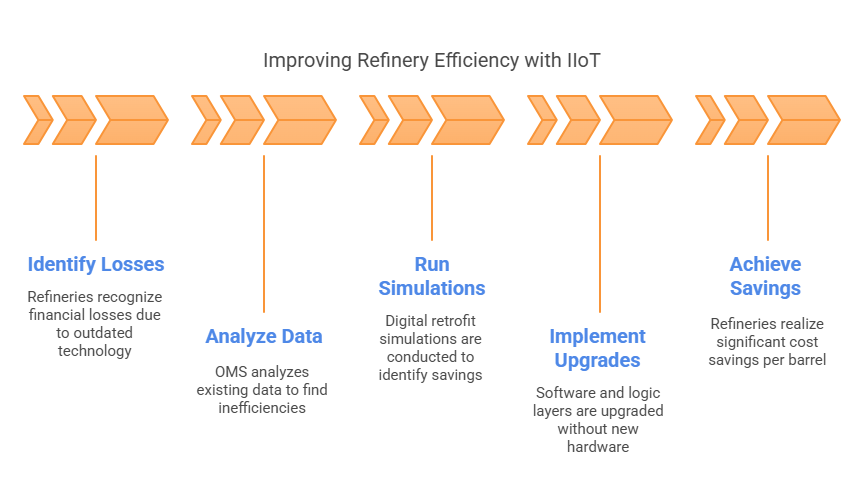
Is Legacy Equipment Blocking Your Refinery Digital Transformation Goals?
While legacy infrastructure may appear reliable on the surface, it often conceals a range of operational inefficiencies and financial liabilities. For refineries, the hidden costs of sticking with outdated systems, especially in bottom-upgrading units and downstream transfer processes, can severely undermine profitability and long-term competitiveness.
What Old Infrastructure Costs You in the Refinery Digital Transformation Journey
Worley’s report on Refinery Bottom-Upgrading underscores a key industry dilemma: many refineries still rely on decades-old heavy oil processing units not designed for today’s crude slates or product quality requirements.
- Older bottom-of-the-barrel units often struggle with low conversion efficiency, higher sulfur content, and more fuel oil production, all of which reduce the recovery of high-value products and cut into margins.
- As the industry shifts toward lighter, cleaner fuels and value-added petrochemicals, outdated infrastructure becomes a significant roadblock.
- These legacy systems are just not built to handle today’s demands, which means refineries can miss out on profitable opportunities—not because of a lack of strategy but because their hardware simply can’t keep up.
OMS tackles this issue through detailed Process Unit Reviews that identify inefficiencies in blending systems, tank farm transfers, and downstream yield management. Instead of recommending costly replacements, OMS engineers focus on logic reengineering, smart integration, and modular retrofits—unlocking performance improvements using the plant’s existing assets. In many cases, margin realization improves simply by re-strategizing how units interact with each other, rather than replacing them outright.
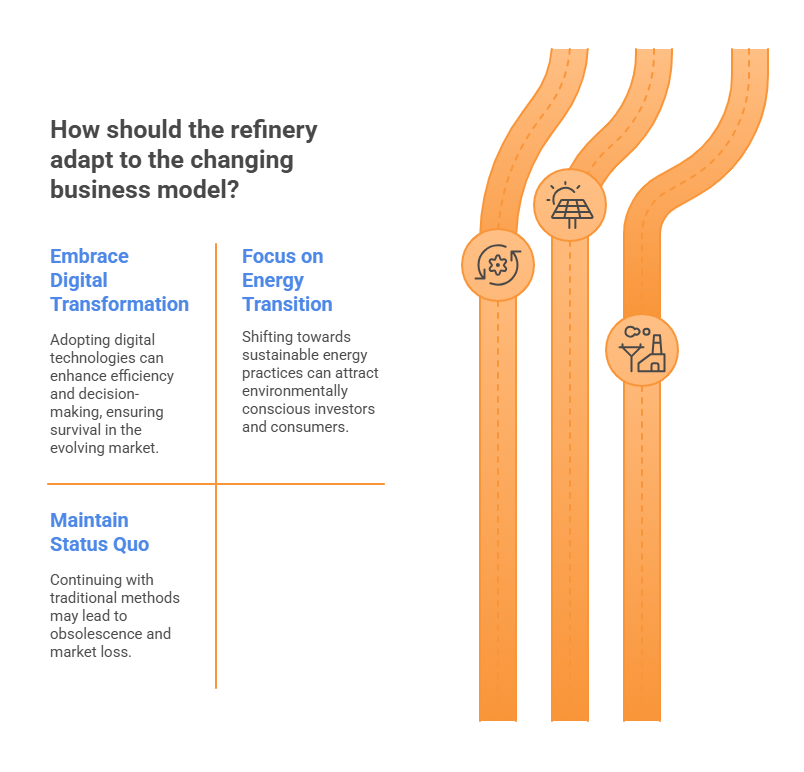
Reducing Safety Risks and Downtime Through Smarter Refinery Digital Transformation
The operational risks of aging infrastructure extend far beyond margins. Energy Career Magazine’s article on Revitalizing Infrastructure highlights that older systems typically require more reactive maintenance, are prone to frequent unplanned outages, and expose operations to higher safety risks due to outdated control logic and poor alarm handling.
- This is especially problematic in off-site systems like blending, tank management, or utilities, where failure in one sub-system can cascade into plant-wide disruptions.
- Moreover, aging equipment often lacks modern systems’ diagnostics and predictive maintenance capabilities, resulting in costlier failures and slower recovery times.
OMS offers targeted upgrades to control logic to tackle these challenges without replacing entire systems.
- These include optimizing PLC/DCS systems, updating interlocks, and cleaning up alarm overload.
- By redesigning how control sequences work and reducing unnecessary alerts, OMS helps operators stay focused and avoid potential shutdowns before they happen.
- These upgrades boost uptime and throughput while making the workplace safer, especially in critical areas like blending and utility balancing, where small mistakes can have significant consequences.
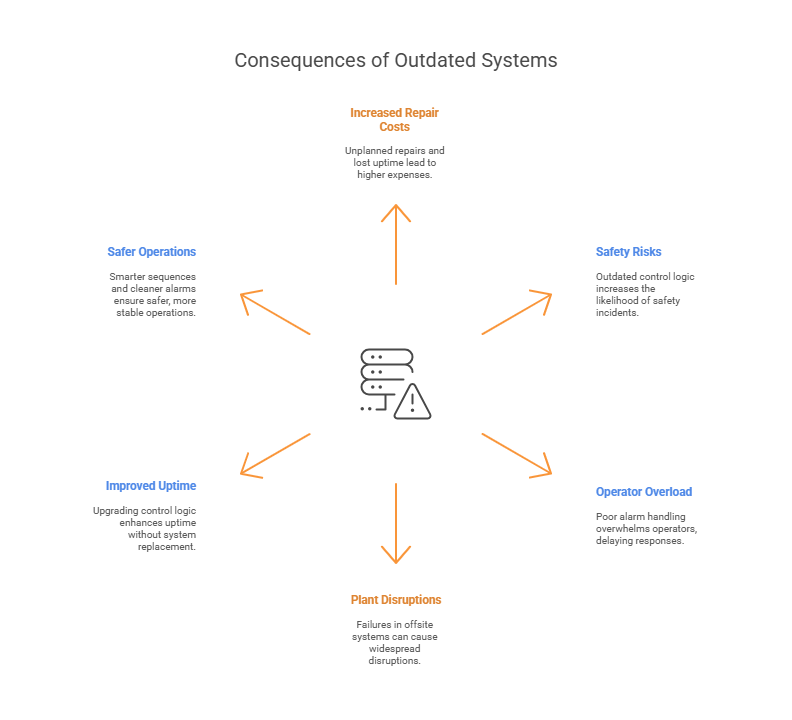
Digital Twins, Retrofits & ROI: Smart Ways to Approach Refinery Digital Transformation
Contrary to popular belief, modernization doesn’t always require massive capital expenditures or shutdowns.
Schneider Electric highlights the value of Digital Twins and Advanced Analytics in real-time energy optimization, maintenance prediction, and asset reliability. These technologies are modular, easily integrable, and often pay for themselves within 12–18 months.
OMS’s Smart Digital Retrofit Model
OMS specializes in noninvasive retrofits, overlaying smart sensors, AI-driven control loops, and tank blend optimizers without touching the core infrastructure. The result? Improved yield, optimized steam distribution, and minimized tank heel loss.
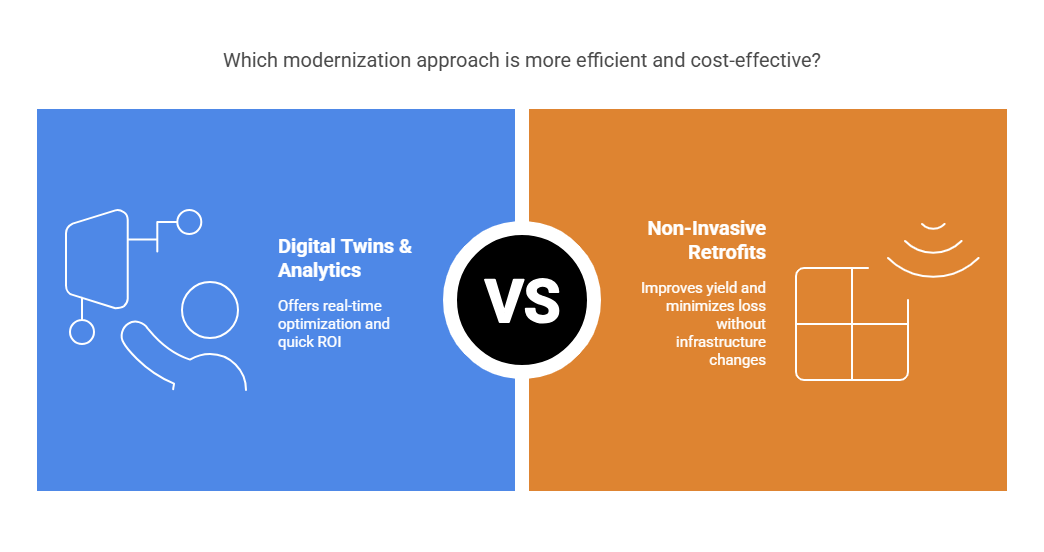
Refinery Digital Transformation with Predictive Maintenance Pays Off Long-Term
AspenTech’s case study shows that predicting pump failures over 35 days in advance can save up to $30 million by giving operators time to act without disrupting production. Building on this proven value, OMS takes a collaborative approach to rolling out Predictive Maintenance (PdM).
By working closely with condition-monitoring partners, OMS helps design innovative sensor placement strategies, build effective data analysis pipelines, and integrate insights directly into the reliability-centered design of off-site units. The result is a seamless PdM ecosystem that doesn’t just prevent failures—it enhances long-term efficiency and equipment health. So, why wait for a breakdown when you can predict it?
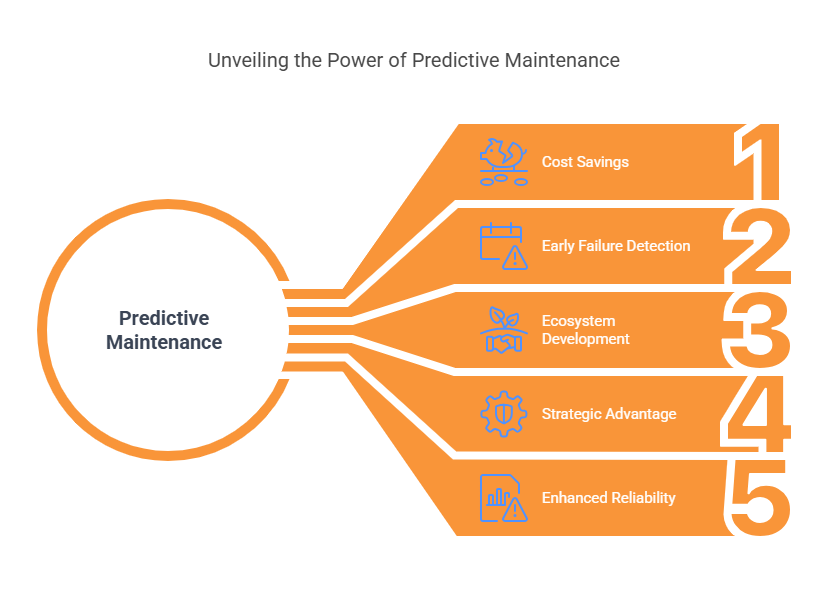
Can’t Afford a Major Overhaul? Budget-Friendly Paths to Refinery Digital Transformation
For many refineries, the most significant barrier to modernization isn’t lack of intent—it’s the perceived financial disruption. Full-scale overhauls often have high CAPEX, prolonged downtimes, and operational risk. But as Shell Global’s experience with Refinery Revamps demonstrates, a more pragmatic alternative is modular, phased upgrades that deliver value incrementally while preserving day-to-day operations.
Modular Upgrades: A Practical Strategy for Refinery Digital Transformation
Shell’s revamp strategy is an excellent example of how targeted, step-by-step improvements can boost performance and cut costs without shutting down an entire plant. Whether upgrading a crude distillation unit or adding energy-saving features, Shell’s modular approach keeps operations running while modernizing systems in manageable stages. This avoids the disruption of complete shutdowns and makes planning upgrades around production schedules and budget limits easier, which helps maximize ROI.
For refineries with tight budgets or those cautious about changing long-standing processes, this phased approach offers a smart, practical path forward: steady improvements without significant interruptions.
- OMS follows the same logic with its Phased Implementation Model, delivering modular upgrades like blend model tuning, tank automation, and alarm management based on each client’s goals and funding.
- Each phase is designed to stand alone, so refiners immediately see real results while pursuing long-term digital growth.
- It’s a flexible way to reduce disruption, control costs, and progress toward full digital maturity—one step at a time.

Training Your People Is the Backbone of Any Refinery Digital Transformation Plan
Technology alone doesn’t transform a refinery—people do. Even the most advanced digital systems can underperform if operators aren’t confident using them or if institutional culture resists change. That’s why embedding a robust training strategy into every upgrade is essential for implementation success and long-term return on investment.
Building capability through eLearning
The OMS eLearning Academy is a refinery-specific, on-demand training platform that helps teams prepare for digital transformation from the ground up. Its simulation-based courses are built around real-world refinery scenarios—from tank farm automation to offsite control strategies—and they’re accessible anytime, on both desktop and mobile devices.
What sets the OMS Academy apart is its modular learning structure. Operators can learn at their own pace, supervisors can monitor progress, and training can start even before new systems are fully rolled out. This proactive approach helps teams get comfortable faster, reduces mistakes during the transition, and ensures that new technology is used well, delivering real value from day one.
“Training shouldn’t be an afterthought. It should be embedded into every stage of the upgrade journey—starting before deployment and continuing beyond it.”
— OMS eLearning Academy
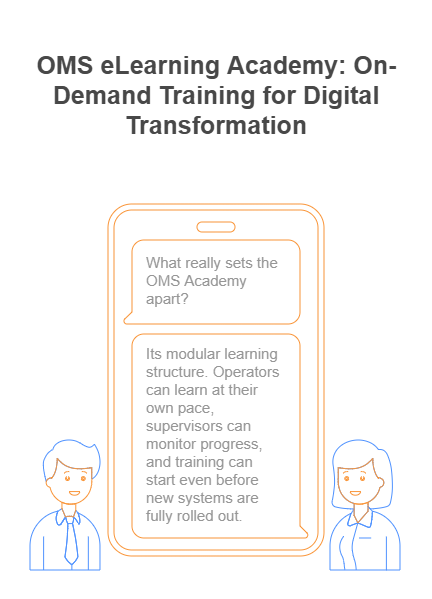
Simulation-Based Learning: The Human Side of Refinery Digital Transformation
Every OMS deployment comes with a customized training plan built around the specific technologies being introduced. These plans include interactive digital simulations, hands-on operator labs, and role-based modules designed to make learning easy to understand and remember.
- The goal is straightforward: ensure teams know how to use new digital tools in their daily decisions.
- By weaving training into the rollout timeline, OMS goes beyond just checking a compliance box—it helps people change how they work.
- This focus on people, not just systems, is why OMS training has such a lasting impact—it is scalable, measurable, and built to last.
A report in the AIChE Chemical Engineering Progress (CEP) journal found that structured, simulation-based training can reduce operator error by over 40% and significantly improve adherence to safety procedures. That’s a powerful way to reduce risk.
OMS takes this even further by creating custom training simulators using actual plant data. This allows staff to practice real scenarios before they happen—whether handling a blending shutdown, managing tank transfers, or executing a steam purge. It’s one of the most effective ways to build confidence and reduce mistakes in high-risk operations.
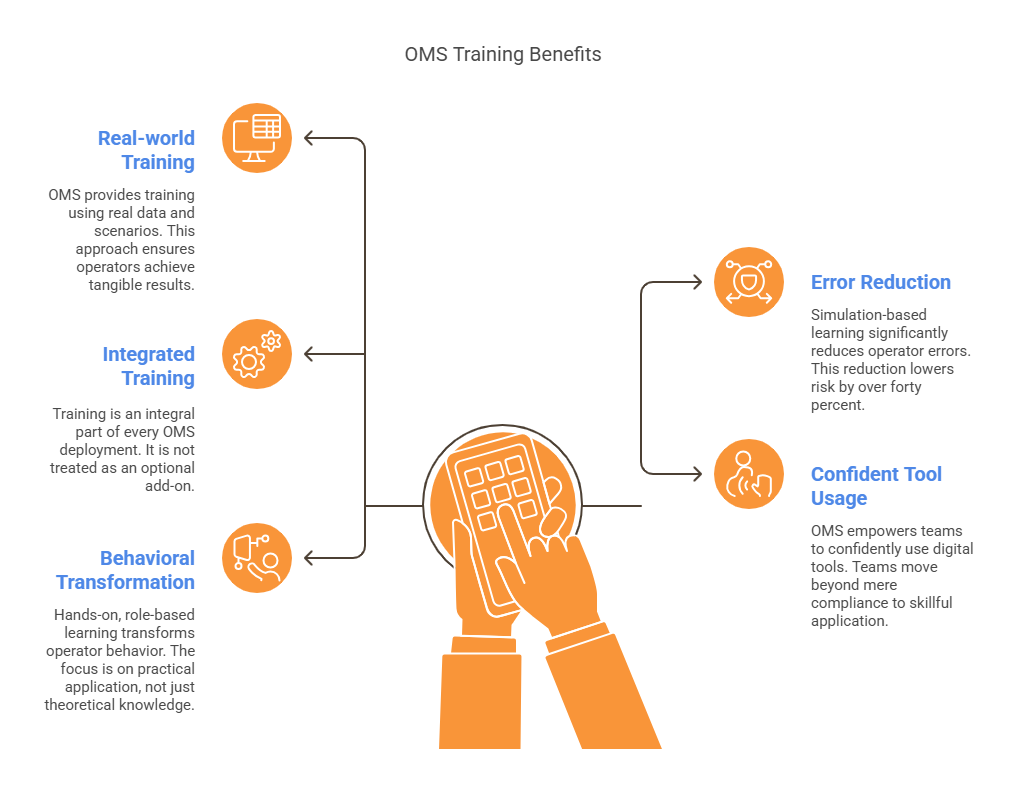
Outdated Systems Are a Liability—Refinery Digital Transformation Makes You Future-Ready
In refineries, every barrel matters. And so does every second of downtime, every unexpected shutdown, and every unoptimized blend. The compounding effect of old technology, poor training, and reactive maintenance is not just a technical concern—it’s a strategic risk.
The good news? Refineries don’t need to leap into full-scale digital transformation. With the right strategy, modular upgrades, and human-centric training, even the most legacy-heavy plant can evolve into a high-performance facility.
OMS is committed to making this transition smart, safe, and ROI-driven.